Режим бурения. Проект строительства скважины с горизонтальным окончанием
Режим бурения
К атегория:
Буровое оборудование
Режим бурения
Общие данные по режиму бурения
Режим бурения определяется буримостыо горных пород (механической скоростью бурения) и проходкой на долото.
Режим бурения выражается пятью основными величинами:
1) давлением долота на забой;
2) числом оборотов долота;
3) количеством промывочной жидкости, прокачиваемой в 1 сек.;
4) давлением на насосе (при турбинном бурении);
5) качеством промывочной жидкости.
Давление долота на забой создается за счет части веса бурильной колонны, однако чрезмерное увеличение нагрузки может привести к поломке инструмента и к искривлению скважины. Во избежание искривления скважины и аварий внизу бурильной колонны устанавливают утяжеленный низ.
При работе с утяжеленным низом его вес используется только на 75%.
Заданная величина нагрузки на долото контролируется гидравлическим индикатором веса.
Индикатор веса ГИВ-2
Индикатор веса ГИВ-2 состоит из трансформатора давления, укрепляемого на мертвом конце талевого каната, указывающего прибора и верньера, записывающего прибора, медных трубок, соединяющих трансформатор давления с указывающим и записывающим приборами, бачка для запасной жидкости, ручного насоса и запорного вентиля. Вся система заполняется жидкостью: в летнее время водой или 1%-ным раствором хромпика в воде для предохранения от коррозии, а зимой незамерзающей жидкостью - смесью воды со спиртом или с глицерином.
Показывающий прибор представляет собой манометр с трубчатой пружиной, шкала указывающего прибора разделена на 100 частей.
Для более точного определения нагрузки на долото служит верньер 8. Шкала верньера занимает всю окружность и разделена на 40 делений без указания цифр. При изменении нагрузки, действующей в талевом канате, до наибольшего значения, соответствующего 100 делениям прибора, стрелка верньера делает пять оборотов. Таким образом, одно деление верньера соответствует половине деления прибора.
Пример. Определить цену одного деления (в кг) по указывающему прибору индикатора веса с верньером (ГИВ-2), если вес бурильного инструмента на крюке 56 делений.
При каждом индикаторе веса имеется свидетельство о тарировке на рабочий талевый канат диаметром 1”, I1/8” или 13/4”, которое необходимо иметь при подсчетах цены одного деления.
Подсчет. В показании указывающего прибора индикатора веса ГИВ-2 по свидетельству тарировки на канате диаметром i1/8” усилие (в кг) на один конец при 50 делениях 5415 кг, а при 60 делениях 6650 кг.
Разность в показаниях усилий между 50 и 60 делениями определится 6650 – 5415 = 1235 кг.
Роторный индикатор веса РИГ-1
Гидравлический роторный индикатор веса предназначен для контроля работы забойного механизма подачи долота по изменению веса инструмента в процессе бурения двух- и трехствольных скважин двумя комплектами бурильных труб.
При пользовании забойным механизмом подачи бурильный инструмент подвешивают при помощи клиньев, установленных в роторе. Вес инструмента через ротор передается на гидравлический поршневой датчик, установленный под ротором в вырубке подроторного бруса; в связи с этим в датчике создается давление, которое измеряется пружинным манометром.
В момент сработки забойного механизма на полную длину хода штока вследствие зависания его на колонне бурильных труб и отрыва долота от забоя вес инструмента увеличивается, что фиксируется стрелкой манометра.
Датчик роторного индикатора веса представляет собой блок из 11 поршней, помещающихся в расточках вытянутого прямоугольного корпуса.
Поршни снабжены резиновыми самоуплотняющимися кольцами, препятствующими вытеканию жидкости из полости цилиндров. Цилиндры сообщаются между собой и заполняются жидкостью через общий штуцер.
Наибольший измеряемый вес инструмента 130 т.
Давление в гидросистеме при максимальном весе инструмента 120 кГ/см2.
Габариты датчика: высота 78 мм, ширина 94 мм, длина 1060 мм.
Габариты приборного шкафа: высота 430 мм, ширина 660 мм, глубина 170 мм.
Вес датчика 28 кг, а приборного шкафа 17 кг.
Числа оборотов долота
Как показала практика роторного бурения, оптимальные числа оборотов трехшарошечных долот, при которых были получены наилучшие результаты по механическим скоростям и проходке на долото, находятся в пределах 200-220 об/мин при бурении в верхних интервалах скважины.
Расход промывочной жидкости
Количество прокачиваемой жидкости зависит от мощности насосной группы бурового оборудования и применяемого бурового инструмента. Современные мощные насосы при спаренной работе позволяют закачивать жидкость в количестве 60 л/сек и более. Однако имеются опасения, что чрезмерное увеличение скорости прокачиваемой жидкости в скважинах, сложенных слабыми породами, приведет к размыву ствола.
Расходомер глипистого раствора РГР-1
Этот прибор предназначен для измерения и записи расхода глинистого раствора на выкиде буровых насосов при бурении скважин.
Расходомер состоит из датчика и вторичного прибора.
Принцип действия прибора
В трубопроводе, по которому протекает измеряемый поток глинистого раствора, ребром к потоку установлен диск, укрепленный эксцентрично на оси.
При движении жидкости скоростной напор потока действует на диск и стремится повернуть его.
Противодействующий момент повороту диска создается спиральной пружиной, связанной с осью, на которую насажен диск. Одновременно при повороте оси измерительного узла ползунок, жестко связанный с осью, перемещаясь по реохорду, изменяет его сопротивление.
Рис. 1. Расходомер глинистого раствора РГР-1.
Расходомер включен в схему автоматического электронного уравновешенного моста ЭМД-207, при помощи которого производятся измерение и запись расхода глинистого раствора.
Режим турбинного бурения
Режим турбинного бурения определяется величиной осевой на* грузки, расходом промывочной жидкости н числом оборотов долота.
В турбинном бурении повышение мощности и вращающего момента на валу турбобура связано с увеличением расхода промывочной жидкости. При увеличении количества прокачиваемой жидкости наряду с увеличением мощностных характеристик турбобура достигается лучшая очистка забоя от выбуренной породы и улучшаются условия работы долота на забое.
С увеличением осевой нагрузки на долото число оборотов вала турбобура уменьшается, а крутящий момент возрастает и при числе оборотов, равном нулю, достигает максимальной величины.
Постепенным изменением осевой нагрузки на долото можно найти такое число оборотов, при котором мощность и к. п. д., развиваемые турбиной, а также механическая скорость проходки будут максимальными.
Выбранную нагрузку даже при бурении в одной и той же породе в связи с износом долота необходимо периодически проверять путем изменения нагрузки на долото.
Турбобуры современной конструкции позволяют работать при нагрузках на долото до 30 т и более.
Числа оборотов долота
Числа оборотов долота в турбинном бурении зависят от количества прокачиваемой жидкости и величины осевой нагрузки.
При долотах современных конструкций наиболее выгодным числом оборотов считается 300-600 обIмин.
При работе в твердых породах необходимо нагрузку на долото увеличивать, а в мягких породах - снижать.
Требования по технологической дисциплине в бурении
1. Основным документом по проводке скважины является геолого-технический наряд (ГТН), обязательный для выполнения буровыми мастерами, бурильщиками и начальниками участков.
2. ГТН составляется на основании утверяеденного типового проекта для каждой скважины индивидуально и утверждается главным инженером и главным геологом предприятия (цех, разведка, контора).
3. Отступление от ГТН в процессе бурения разрешается делать буровому мастеру только по указанию руководства предприятия. Самовольное отступление от технологии проводки скважин начальником участка, буровым мастером или бурильщиком руководством предприятия должно расцениваться как нарушение технологического режима.
4. За три дня до начала бурения новой скважины утвержденный геолого-технический наряд выдается буровому мастеру под расписку. За один день до начала бурения скважины в буровой должно быть проведено производственное совещание - пусковая конференция - под председательством директора предприятия или главного инженера с обязательным участием бурового мастера с бригадой, начальника участка, главного геолога, начальников технического отдела и отдела нормирования, главного механика предприятия, ответственных представителей подсобных предприятий. Докладчиком на пусковой бригадной конференции является буровой мастер, который подробно освещает указания геолого-технического наряда и принятые им меры по оснащению буровой для обеспечения выполнения этих указаний, а также инструкции по уходу за оборудованием, по эксплуатации бурильных труб и предлагает для обсуждения им оперативный график бурения скважины.
5. Пуск буровой без наличия полного комплекта контрольно-измерительной аппаратуры как по контролю процесса технологии бурения, так и по измерению качеств глинистого раствора не разрешается. В комплект контрольно-измерительных приборов на буровой должны входить:
а) индикатор веса (самопишущий и показывающий);
б) амперметры и вольтметры (при наличии электропривода);
в) манометры;
г) аппарат для измерения кривизны скважины системы Пет-росяна;
д) ареометр АГ-1 с ведром и футляром;
е) вискозимер СПВ-5 с мерной кружкой;
ж) отстойник металлический Лысенко ОМ-1 с кружкой. Ответственные буровые (опорные, разведочные и глубокие эксплуатационные) должны иметь переносную лабораторию по глинистым растворам. В буровой направленного турбинного бурения, кроме перечисленных выше, должны быть все приборы и приспособления по визированию: лебедка Яковлева (тяжелая), аппарат Шань-гина или Амбарцумова.
6. В геолого-техническом наряде должны быть заполнены все графы полностью четким почерком тушью. ГТН вывешивается в рамке под стеклом в месте, удобном для пользования буровой бригады.
7. Изменения, намечаемые в технологии бурения, вызываемые в результате полученных дополнительных данных в процессе проводки скважины, а также намечаемые изменения проектных глубин и конструкции скважин должны быть внесены в ГТН.
8. Перед спуском и тампонажем колонн глубиной свыше 1000 м технический отдел предприятия должен вручить буровому мастеру план организации спуска и тампонажа колонны, утвержденный главным инженером предприятия. Анализ тампонажа цемента должен представляться буровому мастеру с первой партией цемента, доставляемой на буровую.
9. Для правильной эксплуатации бурильных и утяжеленных труб должна быть вручена буровому мастеру копия паспорта на трубы. Всякие изменения в комплекте бурильных труб, пройденный метраж, допущенные максимальные нагрузки на них, аварии и причины возникновения их с трубами должны фиксироваться буровым мастером в паспорте.
Промывочные растворы
В качестве промывочной жидкости при бурении нефтяных и газовых скважин применяются глинистые растворы, растворы на нефтяной основе, а также техническая вода. Техническая вода широко применяется в восточных нефтяных районах нашей страны, что позволило улучшить условия работы буровых насосов и сократить расход запасных частей, улучшить очистку промывочной жидкости от выбуренной породы, повысить производительность насосов при меньшем рабочем давлении на выкиде, увеличить мощность турбобура (вследствие чего он стал воспринимать большие нагрузки).
Также увеличились проходка па долото и механическая скорость; сократилось количество подъемов инструмента и расход долот, что позволило повысить коммерческую скорость бурения. При использовании воды в качестве промывочной жидкости необходимо соблюдать следующие условия:
1) переход с воды на глинистый раствор должен осуществляться не ниже чем за 50 м до входа в зону бурения с промывкой глинистым раствором;
2) обеспечить нормальную очистку промывочной жидкости от шлама за счет установки механизмов, вибросит и сит-конвейеров или устройства амбарной системы;
3) перед подъемом инструмента скважину необходимо тщательно промывать;
4) особо уделять внимание замковым соединениям, тщательно следить за смазкой резьбы стойкой мазью и крепить их машинными ключами во избежание промыва резьбы водой.
При переходе с воды на глинистый раствор во избежание прихватов инструмента необходимо тщательно следить за состоянием качества глинистого раствора, не допуская ухудшения его параметров.
Бентонитовый глинопорошок
При бурении нефтяных и газовых скважин в качестве добавки к структурным глинистым растворам, приготовленным из местных глин, а также в качестве основного материала для приготовления промывочных растворов с низким удельным весом и высокими тиксотропными свойствами при бурении в зонах, поглощающих обычную промывочную жидкость (воду или глинистый раствор), применяют порошок из бентонитовой глины.
Бентонитовый порошок приготовляют из бентонитовой глины, не содержащей гипса, мергеля, песка и других вредных примесей.
Качество порошка определяют по параметрам растворов, приготовленных на его основе с дистиллированной водой, а тонкость помола бентонитовой глины - по остатку на сите (4900 отверстий на 1 см2), который не должен превышать 5%.
Характеристика глинистого раствора, приготовленного из порошка бентонитовой глины, должна быть следующая.
Приборы для определения качества глинистых растворов Ареометр АГ-1 для замера удельного веса глинистого раствора.
Для определения удельного веса глинистого раствора необходимо отсоединить стакан от поплавка и заполнить его раствором. Затем следует вставить в него поплавок, после чего ареометр нужно опустить в ведерко с водой. Величину удельного веса определяют по шкале. Ареометром АГ-1 можно измерять удельные веса утяжеленных растворов; для этого необходимо отвинтить съемный груз, а отсчет удельного веса вести по второй шкале.
Рис. 2. Ареометр АГ-1.
1 - жестяная воронка; 2 - калиброванная трубка диаметром 5 мм; 3 - сетка; 4 - кружка с глухой перегородкой, раздели юща я ее на две части объемом 200 и 500 сма.
Рис. 3. Стандартный полевой вискозиметр СПВ-5.
1 - поплавок; 2 - стакан; 3 - съемный грузик.
Вискозиметр СПВ-5
Практически замер производится следующим образом. В воронку наливают поочередно 500 и 200 см3 глинистого раствора, закрыв нижний конец трубки пальцем. Для правильности показаний раствор должен быть процежен через сетку, предварительно вставленную в воронку. Подставив под воронку кружку, отнимают палец от конца трубки, а другой рукой засекают время на секундомере. Время истечения 500 см3 воды из вискозиметра при Ъ-мм трубке равно 15 сек. Величина вязкости измеряется временем истечения 500 смг раствора в секундах.
Автомат для регистрации параметров глинистого раствора АПГР-1
Автомат АПГР-1 предназначен для непрерывного измерения и регистрации удельного веса и вязкости глинистого раствора.
Автомат состоит из шести отдельных узлов, собранных на обгцей раме:
1) циркуляционной камеры; 2) вискозиметра; 3) блока насосов; 4) блока питания воздухом; 5) распределительного щитка; 6) дифманометра.
Центробежный насос из желоба циркуляционной системы подает глинистый раствор в циркуляционную камеиу. избыток глинистого раствора вытекает через сливную трубу 16. Назначение сливной трубы поддерживать постоянный уровень в камере и постоянную скорость движения раствора в измерительном отсеке. В измерительный отсек погружены две пьезометрические трубки, через которые подается воздух.
Воздух от воздуходувки через регулятор давления подается на контрольные стаканчики. Расход воздуха устанавливается регулировочными винтами обычно количество воздуха составляет 120-140 пузырьков, что соответствует расходу 0,7-0,8 л/час через каждую трубку.
Рис. 4. Схема автомата для регистрации параметров глинистою раствора АПГР-1.
1 - контрольные стаканчики; 2 - регулировочные винты; з - циркуляционная камера; 4 - пьезометрические трубкп; 5 - катушка соленоида клапана; 6 - водяной клапан; 7 - самопишущий поплавковый дифманометр; S - электрические часы; 9-таймлер; 10 - вискозиметр СПВ-5; 11 - электроды; 12 - электродвигатель; 13 - воздуходувка; 14 - регулятор давления; 16 - центробежный насос; 1в - сливная труба.
Удельный вес раствора определяется разностью давления, которая измеряется самопишущим поплавковым дифманометром, подключенным параллельно трубкам.
Вязкость раствора измеряется стандартным полевым вискозиметром типа СПВ-5, в который опущены три электрода.
Каждые 10 мин. таймлер замыкает цепь катушки соленоидного клапана, который, срабатывая, открывает доступ раствору в вискозиметр. Когда уровень раствора в воронке коснется верхнего электрода, что соответствует объему 800-1000 см3, клапан автоматически закроется, а приток раствора прекратится. Уровень раствора в вискозиметре начнет понижаться. Когда в вискозиметре останется 700 см3 глинистого раствора, средний электрод перестанет касаться его уровня и включатся электрические часы 8. Когда в вискозиметре останется 200 см3 глинистого раствора, нижний электрод перестанет касаться уровня и прекратится запись времени истечения.
Через 3 мин. после начала цикла измерения вязкости откроется клапан 6, в вискозиметр поступит вода для промывки прибора. Промывка прибора длится 30-40 сек.
Следующий цикл измерения начинается через 6 мин. после окончания предыдущего.
Диапазон измерения удельного веса 1,0-2,0 г/см3, предел измерения вязкости 50-100 сек.
Погрешность измерения удельноговеса ±0,02г/см3, вязкости ±1 сек. Скорость перемещения дисковой диаграммы регистрирующего прибора 1 об /сутки.
Питание автомата: переменным током напряжением 220 в, мощностью 300 ва.
Габаритные размеры автомата 780 X 450 X 750 мм. Вес 130 кг.
Отстойник ОМ-1
Рис. 5. Прибор ЦС-1 для определения стабильности глинистого раствора.
В отстойник наливают 50 см3 глинистого раствора, который затем разбавляют водой до объема 500 см3. Содержимое сильно взбалтывают, после чего прибор ставят в вертикальное положение на 3 мин. Этого времени вполне достаточно для осаждения песка, так как при этом успевают осесть все частицы размером более 0,02 мм. Частицы, не успевшие осесть, являются пылью и на качество глинистого раствора практически влияния не имеют.
Определение стабильности глинистого раствора
Стабильность измеряется следующим образом. Цилиндрический сосуд заполняют глинистым раствором и оставляют в покое па 24 часа. Если вначале раствор в сосуде был однороден, то после стояния в покое его свойства в верхней и нижней частях сосуда становятся различными.
После 24-часового отстаивания глинистый раствор из верхней половины сосуда сливают через боковой отвод, снабженный резиновой трубкой и зажимом, а из нижней половины - через нижний отвод. Измеряют ареометром удельные веса обеих порций раствора. Разность удельных весов обозначается буквой С и принимается за меру стабильности глинистого раствора.
Рис. 6. Металлический отстойник ОМ-1-
Пример. Удельный вес глинистого раствора в верхней половине сосуда равен 1,20, а в нижней 1,24 г/см3\ стабильность при этом будет равна С = 1,24 - 1,20 = 0,04 г/см3.
Чем больше число, показывающее стабильность, тем хуже качество глинистого раствора. Для неутяжеленных глинистых растворов стабильность должна быть не более 0,02, а для утяжеленных не более 0,06 г/см3.
Суточный отстой
Для определения суточного отстоя глинистый раствор наливают в стеклянную мензурку и оставляют в покое на 24 часа. Затем измеряют объем выделившегося из раствора слоя светлой жидкости в процентах по объему от объема глинистого раствора.
Для хороших глинистых растворов суточный отстой равен нулю; вообще он не должен быть выше 2-4%.
Определение статического напряжения сдвига
Статическим напряжением сдвига называется прочность жесткой пространственной структуры, возникающей в глинистом растворе в состоянии покоя вследствие слипания частиц глины.
Так как прочность структуры глинистого раствора возрастает с течением времени, прошедшего с момента окончания перемешивания, было установлено, что измерение следует производить через 1 мин. и через 10 мин. после окончания перемешивания; в этом случае статическое напряжение сдвига обозначается вг и 01О.
Измерение статического напряжения сдвига на приборе СНС-1 осуществляется следующим путем. Глинистый раствор наливают в стакан, установленный на вращающемся столике. Вращение столику передается при помощи кольцеобразной пружины 3 от маленького электродвигателя. После сильного перемешивания раствора в стакане в него погружают цилиндр, подвешенный на кронштейне на тонкой упругой стальной нити. После паузы в 1 или 10 мин. включают двигатель, стакан начинает вращаться со скоростью один оборот за 5 мин. Пока структура в глинистом растворе не разрушена, вращение от стакана передается через слой глинистого раствора, как через твердое тело, цилипдру, который вращается вместе со стаканом. Нить 2 при этом закручивается и сила сопротивления ее дальнейшему закручиванию все возрастает. Но наступает такой момент, когда сопротивление нити преодолевает прочность структуры глинистого раствора у стенок цилиндра и цилиндр останавливается. В этом положении замечают наибольший угол закручивания нити от первоначального положения и по данным, имеющимся в паспорте прибора, рассчитывают соответствующую этому углу закручивания величину статического напряжения сдвига. Для отсчета углов закручивания на приборе установлен лимб.
Рис. 7. Прибор CHG -1 для определения статического напряжения сдвига глинистых растворов.
Для утяжеления считаются пригодными глинистые растворы, имеющие статическое напряжение сдвига в пределах в = 30 4—т- 50 мг/см2.
Определение водоотдачи глинистого раствэра
Измерение водоотдачи на буровых производится при помощи приборов ВМ-6. Образец глинистого раствора объемом 120 см3 заливают в фильтрационный стакан 1. Дно стакана представляет
Рис. 8. Прибор ВМ-6 для определения водоотдачи глинистых растворов.
собой решетку для вытекания отделяющейся жидкости. На эту решетку в качестве пористой перегородки кладут фильтровальную бумагу. Избыток давления на глинистый раствор создается весом плунжера и кожуха с грузовым кольцом, подобранного с расчетом создания избыточного давления в 1 кГ/см2.
Давление плунжера на глинистый раствор передается через машинное масло, заполняющее цилиндр. Объем воды, отжимаемой из глинистого раствора, определяется по опусканию плунжера в цилиндре. Для отсчета на цилиндре сделана метка, а на кожухе прикреплена шкала, деления на которой показывают величину водоотдачи. В нижней крышке сделан запорный клапан, состоящий из стального диска с резиновой прокладкой сверху и нажимного винта. Этот запорный клапан служит для того, чтобы не происходило выделения воды из глинистого раствора во время сборки и регулировки прибора перед измерением.
Прибор ВМ-6 позволяет непосредственно измерять водоотдачу до 40 см3.
К атегория: - Буровое оборудование
Отправить свою хорошую работу в базу знаний просто. Используйте форму, расположенную ниже
Студенты, аспиранты, молодые ученые, использующие базу знаний в своей учебе и работе, будут вам очень благодарны.
Размещено на http://www.allbest.ru/
Режим бурения
Получили распространение три способа бурения нефтяных и газовых скважин: роторный, гидравлическими забойными двигателями и бурение электробурами. Первые два из этих способов -- основные.
Выбор наиболее эффективного способа бурения обусловлен задачами, которые должны быть решены при разработке или совершенствовании технологии бурения в конкретных геолого-технических условиях.
На основании данных, полученных при опытном бурении, сравнивают способы бурения и выявляют из их числа наиболее эффективный для конкретных геолого-технических условий.
В качестве критерия оценки эффективности способа бурения обычно принимают стоимость затрат на 1 м проходки.
Влияние параметров режима бурения на показатели работы долот
Понятие о режиме бурения и его параметрах. Под режимом бурения понимается определенное сочетание регулируемых параметров, влияющих на показатели бурения. К числу таких параметров режима бурения относятся:
- осевая нагрузка (давление) на долото Р д;
- частота вращения долота n;
- количество прокачиваемой промывочной жидкости Q;
- качество промывочной жидкости (плотность, вязкость, показатель фильтрации, статическое напряжение сдвига).
Сочетание этих параметров, позволяющее получать наиболее высокие качественные и количественные показатели бурения при данной технической вооруженности буровой, называется рациональным (или оптимальным) режимом бурения.
На практике часто в процессе бурения приходится отбирать керн, бурить скважину в неблагоприятных геологических условиях (зонах, склонных к поглощениям, осложнениям, связанным с нарушением целостности ствола скважины, и т. п.), забуривать в сторону от ранее пробуренного ствола и т. д. Режимы бурения, применяемые в таких случаях, называются специальными режимами.
Влияние количества и качества бурового раствора. Промысловыми наблюдениями и лабораторными исследованиями установлено, что наилучшие результаты работы долот получают при своевременном удалении с забоя выбуренной породы, в противном случае она оказывает дополнительное сопротивление долоту. Чистота забоя, а следовательно, и собственно процесс бурения зависят от следующих факторов.
1. Качества бурового раствора очистка скважины от мелкого шлама лучше обеспечивается при глинистых растворах с малой вязкостью и малой прочностью структуры. Крупные куски шлама лучше удаляются при густых и вязких растворах. Увеличение плотности повышает подъемную способность глинистых растворов.
Механическая скорость проходки зависит от дифференциального давления, представляющего собой разность между давлением столба бурового раствора в скважине и пластовым (поровым) давлением. Давление столба жидкости (гидростатическое давление) прямо пропорционально ее плотности. Если дифференциальное давление больше 3,5 МПа, то механическая скорость проходки остается примерно постоянной.
С увеличением плотности бурового раствора увеличивается давление на забой скважины, сопротивляемость пород разрушению возрастает, вследствие чего показатели бурения уменьшаются. В тех случаях, когда геологические условия позволяют, следует использовать в качестве бурового раствора воду, газ или воздух с обязательной компенсацией их недостаточной подъемной способности высокой скоростью движения в затрубном пространстве.
2. Количество бурового раствора , подаваемого на единицу площади забоя скважины. Установлено (исследования проводились при бурении роторным способом и электробуром), что технологически необходимое количество промывочного раствора (Q, л/с) примерно равно
где F 3 площадь забоя скважины, см 2 .
Превышение подачи буровых насосов над вычисленной по данному соотношению величиной не приводит к существенному изменению механической скорости проходки.
Скорости истечения потока жидкости из отверстий долота и расположения этих отверстий по отношению к шарошкам и забо ю скважин
С увеличением скорости истечения бурового раствора из долотных насадок улучшается очистка забоя скважины, а следовательно, возрастает механическая скорость проходки. Наблюдения показывают, что значительный рост механической скорости проходки достигается в том случае, когда скорость струй, вытекающих из насадок гидромониторного долота, превышает 6075 м/с. Большое значение на условия очистки забоя оказывает высота зубьев шарошек. Чем больше просвет между шарошками и забоем, тем совершеннее его очистка и выше значения h/n. Наименьшие значения h/n наблюдаются в тех случаях, когда применяются алмазные долота, в которых зубья (алмазы) выступают за матрицу на незначительную высоту, и штыревые с твердосплавными вставками, почти утопленными в теле шарошки.
Влияние частоты вращения долота. При увеличении частоты вращения долота механическая скорость проходки растет, достигая максимальной величины, а затем снижается. Каждому классу пород (пластичные, пластичнохрупкие и хрупкие) соответствуют свои критические частоты вращения долота, превышение которых вызывает снижение механической скорости проходки. Надо также иметь в виду, что повышение частоты вращения шарошечных долот снижает долговечность их работы вследствие более интенсивного износа опор и сокращает проходку за рейс долота.
Рис.10.1. Кривая зависимости механической скорости проходки от ударной нагрузки
Рис. 10.2. Влияние осевой нагрузки на механическую скорость и проходку на долото при турбинном бурении
Влияние осевой нагрузки . Влияние осевой нагрузки на механическую скорость проходки могут быть охарактеризованы графиком (рис. 10.2), отражающим качественную сторону процесса. На кривой выделяются три области. Область I характеризуется тем, что v увеличивается пропорционально увеличению Р д. В этой области удельная нагрузка значительно меньше прочности разрушаемой породы, поэтому процесс разрушения носит поверхностный характер. Область I называется областью поверхностного разрушения.
В области II и также увеличивается с ростом Р д, но в данном случае механическая скорость проходки растет быстрее, чем увеличивается создаваемая на долото нагрузка. В этой области породы разрушаются при удельной нагрузке, меньшей твердости разрушаемой породы, но уже близкой к ней. Эта область условно называется областью усталостного разрушения. На границе областей // и /// удельная нагрузка будет соответствовать твердости разрушаемой породы.
В области III процесс разрушения носит объемный характер. Область /// называется областью нормального или объемного разрушения.
Описанное выше разделение режимов разрушения породы условное, так как при работе долота в разной степени наблюдаются все три вида разрушения.
Взаимосвязь между параметрами режима бурения. В роторном бурении параметры режима бурения не зависят друг от друга. В процессе бурения можно менять любой из них: Р д, n или Q, не изменяя других.
Иное дело в турбинном бурении. Здесь основной параметр режима бурения -- количество прокачиваемого бурового раствора Q, т. е. частота вращения долота в турбинном бурении переменна и зависит от количества бурового раствора и осевой нагрузки на долото, другими словами, при турбинном бурении изменение Q неизменно повлечет за собой изменение n и Р д.
При бурении электробуром также имеются свои особенности. Электробуром практически бурят при постоянной частоте вращения долота, и бурильщик не может ее регулировать. Менять частоту вращения можно только заменой электробура другим двигателем, имеющим иную частоту вращения, изменением частоты тока или при помощи редукторов-вставок.
Изменение мощности, затрачиваемой долотом на разрушение пород, имеющих различные физико-механические свойства, вызывает изменение силы тока в электрической цепи, питающей электробур. Это позволяет следить по показаниям амперметра за характером работы долота на забое, создавать оптимальные осевые нагрузки, определять степень износа долота.
Критерий оценки эффективности применяемых параметров режима бурения. Таким критерием может служить рейсовая скорость проходки или стоимость 1 м проходки, так называемая экономическая скорость.
Разработка параметров режима бурения
Опытное бурение. Разрабатывать рациональное (оптимальные) параметры режима бурения следует на основании проводки опорно-технологических скважин (ОТС). Проводка опорно-технологической скважины предшествует составлению технического проекта. С этой целью необходимо:
1. тщательно изучить геологические условия (стратиграфию, тектонику) района, в котором предполагается бурить, и физико-механические свойства пород;
2. установить зоны возможных осложнений (нарушения целостности ствола скважины, выбросы, поглощения бурового раствора и т. п.), а также определить пластовые давления продуктивных горизонтов;
3. изучить возможности самопроизвольного искривления ствола скважины и профилактические меры, ранее применявшиеся против искривления, а также выяснить эффективность этих мер;
4. в соответствии с геологическими условиями бурения:
a. выбрать буровой раствор, задаться его параметрами для разбуривания отдельных горизонтов (свит и пластов);
b. произвести поинтервальный выбор способа бурения;
c. выбрать типы долот для разбуривания отдельных горизонтов (свит и пластов).
Если бурение проектируется в районе, где ранее не проводилось глубокое бурение, все изложенные выше определения должны быть произведены по результатам бурения в близлежащих геологических сходных районах.
В зависимости от способа бурения, механических свойств пород, качества бурового раствора и избранных типов долот приступают к определению необходимых значений для осевой нагрузки Р д, количества прокачиваемого бурового раствора Q и частоты вращения долота n. При этом следует руководствоваться (независимо от способа бурения) следующими положениями.
1. Потенциальные возможности буровой установки должны быть максимально использованы.
2. Для промывки скважины должен быть выбран буровой раствор с минимально возможными параметрами: плотностью, вязкостью, статическим напряжением сдвига.
3. Количество прокачиваемой жидкости должно быть достаточным для очистки забоя и выноса частиц выбуренной породы (шлама) на поверхность.
Составляются программы проведения исследований по выявлению влияния регулируемых параметров режима бурения на показатели работы долот. Опорно-технологические скважины рекомендуется бурить ротором и электробуром, так как, используя эти способы, можно соблюсти основные условия проведения исследований независимость основных параметров режима бурения (осевой нагрузки и частоты вращения) друг от друга, а также иметь необходимый диапазон изменения частот вращения. Однако эта рекомендация не исключает и проводку их с применением гидравлических забойных двигателей.
В процессе проводки опорно-технологической скважины благодаря созданию различных сочетаний параметров режима бурения находят оптимальные варианты. Обработка данных, полученных при бурении опорно-технологических скважин, достаточно трудоемка, требует специальной подготовки. В последнее время для этого широко используются ЭВМ. Применение вычислительной техники для расчета сложного взаимодействия переменных факторов процесса бурения позволяет более точно регулировать и создавать оптимальные условия для бурения.
Режимно-технологические карты. После завершения обработки материалов по пробуренным опорно-технологическим скважинам составляется типовая режимно-технологическая карта для бурения на данной площади.
Режимно-технологические карты, как правило, состоят из четырех частей:
1) режимной;
2) инструктивной;
3) оперативного графика;
4) общей части.
Режимная часть карты включает для каждого стратиграфического горизонта оптимальный режим бурения. В инструктивной части даются рекомендации по предотвращению возможных осложнений и наиболее эффективные меры по борьбе с ними. В режимной и инструктивной частях карты указываются пути увеличения механической скорости проходки скважины. Чтобы буровая бригада в процессе проходки скважины могла определять, как успешно осуществляется процесс бурения, строится оперативный график, в котором отражаются ожидаемая механическая скорость проходки и предполагаемые затраты времени на все операции по интервалам бурения. В общей части карты приводятся организационно-технические мероприятия обеспечивающие предусмотренную в предыдущих частях карты технологию бурения и ожидаемые показатели проходки скважин
Особенности режима бурения роторным способом. Тип долота должны выбирать в соответствии с «Комплексной методикой классификации горных пород геологического разреза, разделения его на характерные пачки пород и выбора рациональных типов и конструкций шарошечных долот для эффективной разбуривания нефтяных и газовых месторождений»
При выборе режима бурения долотами серий ГНУ и ГАУ нужно учитывать следующее: верхнему уровню осевых нагрузок на долото соответствует нижний уровень частот вращения и наоборот; в пластичных, вязких глинистых, а также слабо сцементированных малоабразивных песчано-глинистых и песчаных породах целесообразно бурить при близких к максимальным частотам вращения и пониженных осевых нагрузках на долото; в песчаных и других абразивных породах, а также трещиноватых и обломочных целесообразно снижать частоту вращения ротора во избежание повышенного износа и разрушения вооружения, герметизирующих элементов опор шарошек, козырьков и спинок лап.
Режим бурения, особенно долотами с твердосплавным вооружением и герметизированными опорами, должен выбираться таким, чтобы не допускалось вибраций бурильной колонны.
Частота вращения ротора должна отличаться от критической частоты вращения, при которой совпадают поперечные и продольные колебания бурильной колонны.
Наиболее опасно применение критической частоты вращения при наименьшей критической длине колонны.
Во многих случаях при бурении в мягких неабразивных породах существенное улучшение показателей работы долот достигается при повышении частоты вращения до 140200 об/мин.
Фактическая осевая нагрузка на долото при повышенной частоте вращения инструмента из-за трения бурильной колонны о стенки скважины и вкладыш ротора оказывается существенно меньше, чем по индикатору веса. Поэтому нагрузку на долото следует корректировать с учетом разницы в показателях индикатора веса при вращении и без вращения колонны.
Осевая нагрузка на долото при бурении с повышенной частотой вращения обычно должна быть уменьшена на 2025 % против величины, создаваемой при низкооборотном режиме в тех же случаях.
Переход на высокооборотный режим вращения бурильной колонны может сопровождаться в отдельных породах обвалами стенок скважины и увеличением момента вращения бурильного инструмента. При возникновении указанных явлений необходимо немедленно тщательно промыть и проработать (на длину ведущей трубы) ствол скважины и только после установления нормальных условий бурения переходить на повышенную частоту вращения ротора.
Не рекомендуется применение повышенной частоты вращения ротора при бурении в твердых породах с промывкой технической водой.
При бурении долотами с герметизированными опорами и твердосплавным вооружением неравномерное вращение и подача долота, резкое торможение и внезапные остановки, толчки и удары, повышенный уровень вибрации приводят к разрушению (поломкам, сколам и т. п.) твердосплавных зубков и преждевременному выходу из строя герметизирующих элементов и опор в целом.
При появлении в процессе бурения вибраций, с целью их подавления необходимо уменьшить осевую нагрузку или изменить частоту вращения ротора.
Если изменение в рациональных пределах указанных параметров не приводит к уменьшению амплитуды колебаний до приемлемого уровня, то это свидетельствует о завышенной моментоемкости долота или недостаточном маховом моменте УБТ для данного сочетания типа долота и разбуриваемых пород. Следовательно, на очередной рейс необходимо использовать долото, характеризующееся меньшей моментоемкостью, или повысить маховый момент УБТ желательно за счет увеличения их диаметра.
Роторный способ бурения в зарубежной практике основной. В нашей стране роторный способ используют при бурении глубоких скважин, а также нижней части разреза скважин средней глубины.
Особенности режима бурения турбинным способом. В турбинном бурении энергия, предназначенная для разрушения породы, подводится к забою потоком бурового раствора. Генератором гидравлической энергии являются буровые насосы, преобразующие механическую энергию привода в гидравлическую энергию потока бурового раствора. Часть энергии потока теряется на преодоление гидравлических сопротивлений в нагнетательной линии, бурильных трубах, замках, долоте и затрубном пространстве. Оставшаяся часть энергии используется в турбине турбобура для преобразования в механическую энергию, которая затрачивается на процесс бурения.
Практически характеристики турбобура можно изменять только ступенчато, применяя на различных участках скважины турбобуры неодинаковых типов. Подача буровых насосов регулируется также только ступенчато путем смены цилиндровых втулок. Основная задача проектирования режима турбинного бурения как раз и заключается в установлении режима работы буровых насосов, подборе типов турбобуров и осевой нагрузки на долото для различных участков ствола скважины таким образом, чтобы получить наиболее высокие качественные и количественные показатели бурения.
Особенности режима бурения с оч исткой забоя воздухом или газом
Одна из особенностей режима бурения с очисткой забоя воздухом или газом -- бурение на сравнительно высоких частотах вращения ротора. В процессе бурения шарошечными долотами пород средней твердости, твердых и крепких при очистке забоя газообразным циркулирующим агентом и при соблюдении других параметров режима бурения частота вращения ротора не должна превышать 100200 об/мин, а при бурении сыпучих и мягких пород 200300 об/мин.
Для обеспечения максимальных показателей бурения при использовании газообразных циркулирующих агентов необходимо соблюдать оптимальное соотношение нагрузки на долото и частоты вращения долота. Это соотношение лучше всего определяется по характеру выноса шлама из выкидной линии. Выбрасываемый на поверхность шлам должен состоять из осколков породы различных размеров (при бурении твердых и крепких пород шарошечными долотами), или скатанных кусочков легких пород, или естественного состояния при сыпучих породах и выходить обильным потоком из выкида.
Количество шламовой пыли должно быть минимальным, так как обильное выделение ее указывает на процесс разрушения истиранием, и для перехода на объемный режим разрушения следует увеличить нагрузку на долото и уменьшить частоту вращения ротора, если она была завышена. Для успешного бурения с газообразными циркулирующими агентами необходимо для каждого конкретного случая устанавливать минимальный предел скорости восходящего потока в затрубном пространстве. Минимальным расходом газообразного циркулирующего агента при бурении следует считать такой, при котором в затрубном пространстве с зазором между бурильными трубами и стенками скважины не менее 1215 мм создается скорость восходящего потока, способная выносить выбуренную породу со скоростью 58 м/с.
Повышение давления в циркуляционной системе при бурении с применением газообразного циркулирующего агента отрицательно влияет на показатели бурения. Вследствие повышения давления в циркуляционной системе объем циркулирующего агента резко сокращается, уменьшается скорость восходящего потока, что приводит к недостаточной очистке забоя, возможному образованию сальников и т. д.
Контроль за параметрами режима бурения
Текущий контроль параметров процесса бурения осуществляется с помощью следующих основных приборов: индикатора веса, манометра, моментомера, тахометра, а также приборов для измерения механической скорости и проходки.
Индикатор веса. Осевая нагрузка на долото в каждый момент определяется при помощи индикатора веса. Этим прибором определяется также нагрузка, действующая на крюк талевой системы. Наибольшее распространение получили гидравлические индикаторы веса.
Контроль за другими параметрами режима бурения. Давление бурового раствора измеряется датчиком, который монтируется на трубопроводе между насосами и стояком или на стояке нагнетательной линии буровых насосов.
Частота вращения ротора измеряется тахометрами различных конструкций. Имеются также приборы по измерению механической скорости проходки и ряд других приборов, регистрирующих и показывающих забойные параметры процессов бурения (частота вращения вала турбобура, пространственное положение забоя скважины и т. д.).
Все описанные приборы входят в комплект системы наземного контроля процессов бурения (ПКБ пульт контроля процессов бурения). Номенклатура параметров, контролируемых пультом контроля процессов бурения, определяется в зависимости от мощности буровой установки.
В последнее время все шире и шире внедряется передача параметров режима бурения на расстояние как при помощи проволочной, так и беспроволочной связи. Это позволяет на диспетчерских пунктах (участках) оборудовать специальные пульты, на которых монтируют показывающие и регистрирующие приборы параметров режима бурения каждой буровой.
Диспетчер (инженер участка) получает возможность круглосуточно следить за работой буровых и при необходимости незамедлительно вносить нужные коррективы в процесс проводки скважин.
В США для оптимизации процесса бурения была проведена отработка системы передачи оперативной информации через спутник связи о процессе проводки скважины с буровой, расположенной в Северном море, в исследовательский центр в городе Тулсе (США), откуда выдавались рекомендации по оптимизации процесса бурения и регулированию параметров бурового раствора.
Телеконтроль забойных параметров бурения. Телеметрия забойных параметров при бурении скважин -- решающий фактор в создании автоматической системы управления процессом бурения.
В результате работ, проведенных у нас и за рубежом создано достаточно большое количество приборов для контроля забойных параметров (под забойными параметрами понимаются напряженное состояние бурильной колонны, частота вращения долота, температура и давление на забое скважины, местоположение ствола скважины в пространстве и т. п.). При этом для связи с поверхностью используются различные виды каналов связи:
1) электропроводный с помощью встроенной в колонну труб линии связи;
2) беспроводные с передачей электрического сигнала по бурильной колонне и горным породам и передачей гидравлических импульсов по буровому раствору, заключенному в бурильной колонне;
3) механический по телу бурильной трубы.
Существует два принципиальных метода передачи сигнала с забоя по каналам связи непрерывный и дискретный. Более удобный и надежный в практических целях второй.
В настоящее время находит все большее признание идея создания автономного забойного двигателя с одновременной регистрацией забойных параметров.
Для телеконтроля комплекса параметров процесса бурения скважин электробурами и состояния двигателей электробуров разработано несколько систем. В этих системах передача телеметрических сигналов в скважине осуществляется по токоподводу электробура. Наибольшее распространение получила телеметрическая система СТЭ.
Наращивание бурильного инструмента и спускоподъемные операции (Технология подготовки к СПО)
Подготовка бурильных труб к эксплуатации. Все трубы и соединительные элементы (замки, соединительные муфты, переводники), предназначенные для работы в скважинах, перед вводом их в эксплуатацию в соответствии с требованиями государственных стандартов, нормалей и технических условий подвергают на трубных базах внешнему визуальному осмотру, инструментальному обмеру основных размеров и проверке качества нарезки резьбы гладкими и резьбовыми калибрами. Особенно тщательно осматриваются и проверяются резьбовые соединения. Резьба должна быть гладкой, без заусениц, задиров и других дефектов, нарушающих ее непрерывность, плотность и прочность.
Трубы и замки, признанные годными после контрольной проверки их качества непосредственно на трубной базе, перед пуском в работу свинчивают и крепят между собой.
Эта операция, требующая определенных условий (тщательной очистки резьбы, ее смазки, селективного подбора деталей и т. д.), должна производиться исключительно на трубных базах. В некоторых случаях может быть допущено навинчивание замков на трубы непосредственно на буровых.
Перед навинчиванием необходимо подобрать замок в трубе по натягу резьбы и по конусности, так как этим улучшается сопряжение резьбы. Замковая деталь, имеющая отклонение конусности по большему диаметру, свинчивается с трубой, имеющей также отклонение конусности по большему диаметру; могут быть свинчены также замок и. труба, имеющие отклонение конусности по меньшему диаметру. При подборе замка к трубе по натягу на трубу, имеющую натяг,резьбы с плюсовым допуском, должна быть навинчена замковая деталь с натягом резьбы, выполненным в пределах минусового допуска, и, наоборот, на трубу, имеющую натяг с минусовым допуском,-- замковая деталь с натягом резьбы, выполненным в пределах плюсового допуска. Соединяемые трубу и замок с номинальной величиной натяга резьбы свинчивают без подбора.
Замки на бурильные трубы могут крепиться в холодном или горячем состоянии. Для получения плотного резьбового соединения и уменьшения трения сопрягающихся поверхностей резьбы при их закреплении перед свинчиванием резьбу трубы необходимо смазать графитовой или цинковой смазкой.
При навинчивании замка следует надеть его на резьбу трубы и, осторожно вращая по ходу резьбы, убедиться, что вершины ниток вошли во впадины резьбы, после чего можно увеличить частоту вращения.
Правильность подбора замка к трубе после ручного навинчивания следует проверить по положению торца трубного конца замка по отношению к последней риске резьбы на трубе. Расстояние от торца замка до конца сбега резьбы на трубе должно быть от 1 до б мм.
Существует три метода крепления замков на бурильные трубы:
1. крепление на буровых с помощью бурильной лебедки;
2. на специальных муфтонаверточных станках;
3. навинчивание вручную предварительно нагретого замка.
В настоящее время принудительное закрепление резьбового соединения трубы -- замок при помощи машины (первые два способа) почти полностью уступили место более совершенному -- креплению замка в горячем состоянии.
Процесс навинчивания и крепления замков в горячем состоянии включает следующие операции. Детали замков, подобранные к трубам, перед навинчиванием подвергают нагреву в специальных нагревательных печах. Пока замковая деталь нагревается, на конце трубы с резьбой, подготовленной для навинчивания нагреваемой детали, на определенном расстоянии от последней риски резьбы в сторону тела трубы наносится керном метка, которая в дальнейшем служит ориентиром при осевом перемещении навинчиваемой нагретой детали замка.
Замковые детали нагревают до определенной температуры (400 0 С).
Перед навинчиванием замка резьбу трубы смазывают соответствующей смазкой. Смазку наносят не на всю резьбу, а только на первые три-четыре нитки, считая от торца трубы. После того как замок нагрет, а резьба на трубе смазана, надлежит вынуть термопару из замка, извлечь замковую деталь из печи и навинтить ее на трубу.
Горячий замок навинчивают на трубу так, чтобы торец его совпал с поставленным на трубу керном. Допускается недовинчивание замковой детали до керна не более 1,5--2 мм.
Чтобы в замке не создавалось чрезмерно высокого напряжения, которое может повлечь за собой разрыв замка, нельзя допускать дальнейшее продвижение детали после совпадения торца с меткой -- керном.
Замок, навинченный в горячем состоянии, при охлаждении прочно схватываясь с трубой, обеспечивает прочность и герметичность соединения. Как показала практика, проверка таких соединений опрессовкой необязательна.
Эксплуатация бурильной колонны. Смонтированные новые бурильные трубы объединяют в комплекты, в составе которых они должны работать до полной амортизации. Комплекты состоят из труб, одинаковых как по диаметру и толщине стенок, так и по длине труб. В комплект включают трубы, изготовленные из одной марки, выполненные одним заводом, и замки одного типа, изготовленные также одним заводом.
Состав комплекта по количеству бурильных труб и длине их не ограничивается. Каждому комплекту бурильных труб присваивается свой порядковый номер, а всем трубам, вошедшим в комплект,-- свои порядковые номера внутри комплекта. Все трубы маркируются. Маркировка включает порядковый номер комплекта; показатель группы прочности стали; последнюю цифру года ввода трубы в эксплуатацию; порядковый номер трубы в комплекте; номинальную толщину стенки в мм (для бурильных труб).
Комплекты труб учитывают и отрабатывают самостоятельно. Перевод отдельных труб из одного комплекта в другой запрещается.
На каждый комплект бурильных и утяжеленных труб заводят паспорт-журнал, в котором учитываются все трубы данного комплекта. Паспорт составляют в одном экземпляре и хранят на трубной базе. Паспорт действует до списания всех труб комплекта в материал.
В процессе работы труб в скважинах в паспорт-журнал вносят отметки о ремонте, авариях и о списании отдельных труб, а также указывают номера скважин, в которых работал комплект, длину части комплекта, участвовавшего в проходке каждой скважины, время работы труб, проходку по скважинам и сумму начисленного износа.
Производительной работой бурильных труб, участвующих в бурении скважин, считается проходка в метрах, а для труб ловильных комплектов -- количество скважин, в которых они работали. На трубы, участвующие в проходке скважин, начисляется условный износ в килограммах и рублях, определяемый исходя из количества пробуренных метров в данной скважине.
Бурильные трубы, разбитые на комплекты и отмаркированные, доставляются на буровую. Буровая бригада, непосредственно эксплуатирующая трубы, замки и другие детали, тщательно проверяет качество труб, ведущие трубы, доставляемые в буровую, и соответствие их паспортным данным. Буровой мастер при доставке труб на скважину одновременно получает выписку из паспортов-журналов с отрывными талонами и извещениями о получении комплектов труб. Трубы, замки, соединительные муфты, имеющие наружные дефекты (плены, трещины, кривизну и т. д.), не подлежат приемке. Обнаруженные детали с износом, выходящим за пределы норм (допустимая сработка наружной поверхности бурильных замков по диаметру при равномерном износе для ЗН-80 не более 5 мм; ЗН-95 и ЗН-108--6 мм; ЗН-140--7 мм; ЗН-172--8 мм; ЗН-197--9 мм; ЗШ-108 --8 мм; ЗШ-118 --9 мм; ЗШ-146--10 мм; ЗШ-178 -- 11 мм; ЗШ-203--12 мм; ЗУ-155 --7 мм; ЗУ-185 --8 мм), бракуются и отправляются на трубную базу.
После того как комплекты бурильных труб завезены на буровую, осмотрены и приняты буровым мастером, буровая бригада укладывает их на мостки. Отсюда их берут в процессе бурения для сборки в свечи. Затаскивая трубы в фонарь вышки или подавая свечи из-за пальца, следует предохранять резьбу ниппеля от ударов о ротор и другие металлические предметы.
При свинчивании резьбы в процессе спуска колонны бурильных труб нельзя допускать ударов ниппеля наращиваемой трубы о резьбу муфты трубы, спущенной в скважину. Во избежание самоотвинчивания и разъединения замковой резьбы при бурении забойными гидравлическими двигателями все замковые соединения закрепляют машинными ключами.
При спуске труб в скважину следует не допускать резкого торможения колонны или посадку элеваторов на ротор с ударом, так как это приводит к возникновению больших динамических нагрузок и нередко к авариям.
С целью равномерного износа замковой резьбы следует при подъеме свечей менять положение средних (неразъемных) замковых соединений с концами (разъемными). При роторном бурении, чтобы предохранить бурильные трубы от истирания и от быстрого износа, на них нужно надевать предохранительные кольца-протекторы. Их надевают на бурильные трубы вблизи замка. Благодаря тому, что диаметр предохранительного кольца больше диаметра замка, соприкосновение и трение замков труб об обсадные трубы и стенки скважин устраняются, так как резиновое кольцо исполняет роль упругой подушки.
При любом способе бурения необходимо строго руководствоваться нормами осевых нагрузок на долото, указанными в ГТН.
После окончания бурения скважины при разборке свечей следует все трубы в замковой резьбе развинтить. Также отвинчивают все имеющиеся в колонне переводники, в том числе и предохранительный на ведущей трубе. Разобранные трубы укладывают на мостки аккуратно рядами по комплектам и обильно смазывают резьбу. Нельзя сбрасывать трубы с мостков на землю, транспортировать волоком и т. д. Ответственность за правильную эксплуатацию всех элементов бурильной колонны лежит на буровом мастере, который не должен допускать нарушений технических правил обращения с инструментом. бурение долото забой скважина
Эксплуатация ЛБТ имеет некоторые особенности. В случае недостаточной интенсивности заполнения бурильной колонны (при ее спуске) буровым раствором устанавливается один или несколько перепускных клапанов. Запрещается применять кислотные (грязевые) ванны для освобождения прихваченного инструмента. Концентрация водородных ионов (рН) в буровом растворе должна быть не более 11.
Конструкция подсвечника должна предотвращать образование внутри труб ледяных пробок (замерзание части стекающего раствора в концах труб). Запрещается нанесение каких бы то ни было рисок или меток на тело труб (кроме предусмотренных маркировкой). При проводке скважины с целью достижения равномерного износа всех замковых соединений после каждых очередных 20 спуско-подъемных операций следует менять месторасположение разъемных и неразъемных замковых соединений, строго соблюдая последовательность этой замены.
Для защиты ЛБТ от износа обязательно применение предохранительных колец-протекторов.
Размещено на Allbest.ru
...Подобные документы
История бурения нефтяных и газовых скважин, способы их бурения. Особенности вращательного бурения. Породоразрушающие инструменты (буровые, лопастные, алмазные долота). Инструмент для отбора керна. Оборудование для бурения, буровые промывочные жидкости.
курсовая работа , добавлен 27.09.2013
Схема колонкового бурения с применением буровой установки. Конструкция, назначение и классификация буровых вышек, буров, труб, долот. Причины аварий при различных способах бурения, способы их ликвидации. Режимы бурения нефтяных и газовых скважин.
реферат , добавлен 23.02.2009
курсовая работа , добавлен 22.05.2009
Изучение особенностей алмазного долота для бурения пород малой, средней и высокой абразивности. Основные элементы и рабочие органы алмазных долот и бурильных головок. Применение в производстве импрегнированных и термоустойчивых поликристаллических долот.
презентация , добавлен 05.12.2014
Назначение, устройство основных узлов и агрегатов буровых установок для глубокого бурения нефтегазоносных скважин. Конструкция скважин, техника и технология бурения. Функциональная схема буровой установки. Технические характеристики буровых установок СНГ.
реферат , добавлен 17.09.2012
Проходка скважин станками шарошечного бурения. Буровой инструмент станков шарошечного бурения. Очистные комплексы и агрегаты для добычи полезного ископаемого. Условия применения очистных комплексов, их основные виды и характеристика особенностей.
реферат , добавлен 13.10.2013
Задачи, объёмы, сроки проведения буровых работ на исследуемом участке, геолого-технические условия бурения. Обоснование выбора конструкции скважин. Выбор бурового снаряда и инструментов для ликвидации аварий. Технология бурения и тампонирование скважин.
курсовая работа , добавлен 20.11.2011
Общие сведения о выемочных комбайнах. Основные технологические схемы механизации очистных работ. Схемы перемещения машин вдоль забоя. Врубовые машины и широкозахватные комбайны. Преимущества струговой выемки. Проходка скважин станками шарошечного бурения.
реферат , добавлен 25.08.2013
Проблема сезонности бурения. Специальные буровые установки для кустового строительства скважин, особенности их новых модификаций. Устройство и монтаж буровых установок и циркулирующих систем. Характеристика эшелонной установки бурового оборудования.
курсовая работа , добавлен 17.02.2015
Технические средства направленного бурения скважин. Компоновки низа бурильной колонны для направленного бурения. Бурение горизонтальных скважин, их преимущества на поздних стадиях разработки месторождения. Основные критерии выбора профиля скважины.
Под режимом бурения понимается определенное сочетание параметров, влияющих на показатели бурения. К числу таких параметров относятся:
2) частота вращения долота;
3) массовый расход прокачиваемой промывочной жидкости;
4) качество промывочной жидкости (плотность, вязкость, водоотдача, статическое напряжение сдвига).
Сочетание этих параметров, позволяющее получать наиболее высокие качественные и количественные показатели бурения при данной технической вооруженности буровой, называется рациональным (или оптимальным) режимом бурения.
На практике часто в процессе бурения приходится отбирать керн, бурить скважину в неблагоприятных геологических условиях (зонах, склонных к поглощениям, осложнениям, связанным с нарушением целостности ствола скважины и т. п.), забуривать в сторону от ранее пробуренного ствола и т. д. Режимы бурения, применяемые в таких случаях, называются специальными режимами.
Эффективность работы долота оценивается двумя параметрами:
1) механической скоростью бурения v m е x ′ м/ч;
2) проходкой на долото h,м.
При выборе режима бурения следует учитывать, что с изменением одного из параметров не всегда увеличиваются механическая скорость проходки и проходка на долото. Для каждой породы существует оптимальное сочетание нагрузки на долото, частоты вращения долота и расхода промывочной жидкости.
При турбинном способе бурения изменение одного параметра режима бурения вызывает автоматическое изменение других. В случае увеличения расхода промывочной жидкости при неизменной нагрузке на долото частота вращения n вала турбобура (долота) растет прямо пропорционально. Если же нагрузка на долото будет увеличена, а расход промывочной жидкости останется постоянным, то частота вращения вала турбобура (долота) уменьшится.
В практике бурения скважин расход промывочной жидкости устанавливают с учетом обеспечения наивыгоднейших условий работы турбобура и наибольшего выноса выбуренной породы. С углублением скважины в связи с уменьшением ее диаметра расход промывочной жидкости уменьшают от интервала к интервалу .
При бурении в интервале, для которого установлен постоянный расход жидкости, из трех параметров режима бурения можно изменять только нагрузку на долото, регулируя тем самым частоту его вращения. Последняя при постоянным расходе промывочной жидкости достигает своего максимума при снятии нагрузки на долото.
При создании нагрузки на долото частота вращения вала турбобура (долота) уменьшается, а вращающий момент увеличивается. Эффективная работа турбобура будет обеспечена при таких нагрузках на долото, когда мощность на валу турбобура N достигнет максимального значения. В этот период частота вращения вала турбобура составляет примерно половину частоты вращения долота при отсутствии на него нагрузки, а вращающий момент около половины момента, развиваемого при торможении вала турбобура. При максимальной мощности на валу турбобура турбина имеет и максимальное значение КПД.
Нагрузка на долото зависит от твердости проходимости пород. При разбуривании твердых пород в целях повышения эффективности работы долота повышают нагрузку, а при бурении в мягких породах - снижают. В то же время частота вращения долота в первом случае уменьшается, а во втором - увеличивается, что и требуется для достижения хороших показателей его работы.
При работе турбобуров в соответствии с описанными условиями обеспечиваются наилучшие показатели работы долота, так как повышение и снижение частоты вращения долота приводит к неустойчивому режиму работы турбобура.
При роторном бурении отсутствует ярко выраженная взаимосвязь параметров режима бурения и, следовательно, влияние их друг на друга, как при турбинном способе. Поэтому можно устанавливать любые комбинации параметров режима бурения, контролировать их .
Расход промывочной жидкости устанавливается с учетом качественной очистки забоя скважины. Нагрузка на долото и частота его вращения устанавливаются для каждого геологического горизонта с учетом твердости проходимых пород.
Подача бурильной колонны - вертикальное перемещение на поверхности, которое осуществляется опусканием ведущей трубы в ротор на некоторую величину в результате ослабления тормоза лебедки.
Давление долота на забой создается частично весом бурильной колонны, однако чрезмерное ее увеличение может вызвать поломку бурильной колонны и искривление скважины. Во избежание этого нижняя часть бурильной колонны выполняется утяжеленной.
При работе с утяжеленным низом его вес используется только на 75 %.
Для контроля за равномерным давлением на долото пользуются прибором, называемым индикатором веса. Давление промывочной жидкости измеряется датчиком, который монтируется на трубопроводе между насосами или на стояке нагнетательной линии буровых насосов. Частота вращения ротора измеряется тахометрами различных конструкций. Кроме того, применяют приборы для определения механической скорости бурения, а также другие приборы, регистрирующие и показывающие параметры бурения на забое (частота вращения вала турбобура, пространственное положение забоя скважины и т. д.).
В последнее время все шире внедряется передача параметров режима бурения на расстояние. Это позволяет на диспетчерских пунктах (участках) оборудовать специальные пульты, на которых монтируют показывающие и регистрирующие приборы параметров режима бурения каждой буровой. Диспетчер (инженер участка) получает возможность круглосуточно следить за работой буровых и при необходимости незамедлительно вносить нужные коррективы в процесс проводки скважины.
Технологическим режимом бурения называется сочетание ряда основных задаваемых параметров, характеризующих скоростные и качественные показатели бурения, связанных с разрушением горных пород на забое скважины и выносом выбуренной породы на поверхность.
Основными параметрами режима бурения являются:
Осевая нагрузка на породоразрушающий инструмент;
Скорость вращения бурового инструмента;
Количество и качество промывочной жидкости;
Тип породоразрушающего инструмента.
Осевая нагрузка на породоразрушающий инструмент характеризует параметр режима бурения, определяющий усилие, приложенное по оси бурильной колонны к породоразрушающему инструменту.
Осевая нагрузка на долото в процессе бурения создается весом утяжеленных бурильных труб и колонной бурильных труб.
Режим объемного разрушения породы возможен, если удельное давление на забой превышает сопротивление породы на вдавливание. Таким образом, осевая нагрузка пропорциональна прочности горных пород. Отсюда следует, что при прочих равных условиях наименьшие нагрузки на забой допускаются при бурении мягких пород, с повышением твердости пород осевая нагрузка должна увеличиваться.
При повышении осевой нагрузки на долото механическая скорость бурения увеличивается до определенного критического значения. Сначала скорость возрастает интенсивно, а затем ее рост постепенно замедляется и наступает момент, когда рост прекращается, и скорость начинает уменьшаться. При этом большое значение имеет очистка забоя скважины.
Повышение осевой нагрузки увеличивает проходку на долото и механическую скорость при условии увеличения скорости циркуляции промывочной жидкости, необходимой для полной очистки забоя от выбуренной породы.
При бурении для каждых конкретных условий существует критическое значение осевой нагрузки на долото, которое не может обеспечить дальнейшее повышение скорости бурения. Значение критической нагрузки зависит от физико-механических свойств разбуриваемых пород, а также типа долота.
Оптимальные осевые нагрузки на долото подбираются с учетом полученных результатов отработки долот с различными осевыми нагрузками в зависимости от крепости пород, типа и размера долот, бурильного инструмента и способа бурения.
Повышение механической скорости при увеличении осевой нагрузки, создаваемой на забое весом бурильных труб, без применения утяжеленных бурильных труб не может быть обеспечено. В этом случае от излишней нагрузки бурильные трубы изгибаются, волной изгиба упираются в стенки скважины, чем поглощается большая часть осевой нагрузки и не обеспечивается повышение механической скорости.
Для получения более высокой механической скорости и проходки на долото практикуется создавать наибольшую осевую нагрузку в начале механического бурения. Процесс бурения должен проводиться таким образом, чтобы во время работы долота удельное давление поддерживалось постоянным, а суммарная нагрузка изменялась в необходимых пределах. Бурильный инструмент должен подаваться равномерно и непрерывно с обеспечением необходимой осевой нагрузки по индикатору веса.
Скорость вращения долота
При выборе параметров режима бурения учитывают, что скорость проходки возрастает пропорционально повышению скорости вращения долота при одновременном увеличении осевой нагрузки.
При увеличении скорости вращения повышается износ долота. По достижении определенного числа оборотов износ долота увеличивается быстрее, чем повышается скорость проходки. Влияние скорости вращения долота на эффективность разрушения породы зависит от осевой нагрузки, степени очистки забоя, физико-механических свойств породы и глубины скважины.
Опыт бурения в твердых породах показывает, что для повышения скорости проходки необходимо применять меньшее число оборотов при одновременном увеличении осевой нагрузки на породоразрушающий инструмент.
Скорость вращения долота рекомендуется снижать с увеличением диаметра долота, с повышением твердости и абразивности пород, с уменьшением диаметра бурильных труб, а также при бурении чередующихся пластов небольшой мощности и при переходе из пласта меньшей твердости в пласт большей твердости. Для расчета допустимой скорости вращения для каждого размера бурильных труб применяют формулу:
n - допустимая скорость вращения в об /мин;
l - длина вращающихся бурильных труб в м;
Е - модуль упругости;
g - ускорение силы тяжести, равное 9,8 м/сек2;
q - вес 1 м бурильных труб в кг.
При выборе скорости вращения долота учитывают интервал глубины бурения. С увеличением глубины скважины скорость вращения долота при роторном способе снижают.
Промывка скважины
Процесс очистки забоя скважины от шлама и охлаждения породоразрушающего инструмента буровым раствором называется промывкой скважины.
Практикой бурения и специальными исследованиями установлено влияние параметров промывочной жидкости на качественные показатели бурения.
К числу основных параметров промывки скважины, оказывающих влияние на качественные показатели бурения, относятся: удельный вес, вязкость промывочной жидкости, а также количество подаваемой на забой промывочной жидкости и скорость восходящего потока в затрубном пространстве.
Увеличение удельного веса промывочной жидкости приводит к снижению механической скорости, и, наоборот, при прочих равных условиях скорость проходки повышается при использовании промывочной жидкости меньшего удельного веса.
Промывочные жидкости с меньшей вязкостью лучше очищают забой от разбуренных частиц породы и при условии повышения скорости движения в затрубном пространстве обеспечивают интенсивный вынос их на поверхность.
С повышением количества подаваемой на забой промывочной жидкости увеличивается скорость циркуляции в затрубном пространстве, и при соответствующем изменении параметров режима бурения повышается скорость проходки. При этом существенное влияние оказывают физико-механические свойства пород, тип и размер долота, качественные параметры промывочной жидкости.
С повышением скорости восходящего потока промывочной жидкости в затрубном пространстве увеличивается интенсивность очистки забоя скважины от выбуренной породы, облегчается работа долота на забое и повышается эффективность бурения.
Кроме очистки забоя от выбуренных частиц, промывочная жидкость принимает участие в разрушении пород путем гидромониторного эффекта, который является технической основой для долот с гидромониторной промывкой.
При увеличении осевой нагрузки, скорости вращения и диаметра долота для очистки забоя необходимо повышать количество подаваемой в скважину промывочной жидкости. Таким образом, расход промывочной жидкости находится в прямой зависимости от объема разбуриваемой породы в единицу времени. При недостаточной интенсивности промывки очистка забоя от шлама ухудшается и снижается механическая скорость бурения.
Показателем нормальных условий промывки забоя является скорость движения восходящей струи в кольцевом пространстве между стенкой скважины и поверхностью бурильных труб, имеющая значения от 0,8 до 1,5 м/сек.
В зависимости от скорости циркуляции промывочной жидкости в скважине необходимую производительность насоса определяют по формуле:
Q - производительность насоса в м3/сек;
V - скорость потока промывочной жидкости в м/сек;
F - площадь кольцевого сечения скважины в м2.
Площадь кольцевого сечения скважины рассчитывают по формуле:
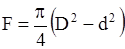
D - фактический диаметр скважины в м;
d - наружный диаметр бурильных труб в м.
При выборе параметров режима бурения необходимо полно использовать установленную гидравлическую мощность буровой установки, бурить при максимально допустимых по геолого-техническим условиям количествах промывочной жидкости. При этом следует учитывать допустимые рабочие давления буровых насосов и увеличение гидравлических сопротивлений с ростом глубины скважины.
Тип породоразрушающего инструмента
Инструментом, предназначенным для механического разрушения породы при бурении, является буровое долото.
В зависимости от физико-механических свойств разбуриваемых пород применяют различные типы и конструкции долот. Долота для вращательного бурения различаются как по назначению, так и по принципу их действия на породу.
По своему назначению буровые долота подразделяются на три группы:
Долота сплошного бурения, разрушающие породу при бурении в скважине сплошным забоем, по всей его площади;
Долота колонкового бурения, разрушающие породу в скважине кольцевым забоем, с оставлением в центре неразбуренного столбика (керна) проходимой породы;
Долота специального назначения, применяемые для различного вида работ в скважине, непосредственно не связанных с процессом бурения скважины (расширения ствола, разбуривания цементного камня и др.).
По принципу воздействия на породу буровые долота разделяются на две группы: долота режущего типа, разрушающие породу в основном резанием, к этому типу долот относятся фрезеры, алмазные; долота скалывающего и дробящего типа, которые разрушают породу в результате скалывающего и дробящего воздействия, к ним относятся все разновидности шарошечных долот.
Долота шарошечные. Шарошечным называется долото, разрушающее горную породу перекатывающимися по забою шарошками. Шарошка - породоразрушающая деталь шарошечного долота, имеющая форму цилиндра или конуса. Боковая поверхность шарошки имеет зубья или твердосплавные вставки (штыри), которые разрушают породу при вращении долота.
Шарошечные долота предназначаются для бурения вращательным способом скважин с промывкой забоя жидкостью или продувкой воздухом. Эти долота применяются для бурения пород с различными физико-механическими свойствами. В зависимости от разбуриваемых пород шарошечные долота для бурения сплошным забоем выпускаются следующих восьми типов:
М - для самых мягких и вязких;
МС - для мягких пород с пропластками пород средней твердости;
С - для пород средней твердости;
СТ - для пород средней твердости с пропластками твердых и абразивных пород;
Т - для твердых и абразивных пород;
ТК - для твердых пород с пропластками крепких и абразивных пород;
К - для крепких, хрупких и абразивных пород;
ОК - для самых крепких и абразивных пород.
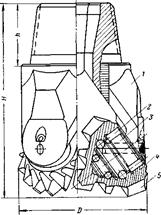
Рисунок 2.6 - Долото трехшарошечное
В зависимости от числа шарошек долота выпускаются одношарошечные, двух-, трех-, четырех- и пятишарошечные долота.
Трехшарошечные долота (рис. 2.6), имеющие конические шарошки и обладающие высокой эффективностью, наиболее распространены при бурении эксплуатационных скважин. По конструктивному исполнению трехшарошечные долота разделяются на бескорпусные (секционные) и корпусные.
Бескорпусное долото состоит из трех сваренных между собой секций. Каждая секция состоит из лапы 1 с цапфой 3, на которой смонтирована шарошка 4 с зубьями 5, свободно вращающаяся на подшипниках качения 2. Бескорпусные долота имеют присоединительную замковую резьбу, которая нарезается после сварки лап. Бескорпусные долота выпускаются диаметром от 76 до 346 мм.
Долота корпусные большого диаметра имеют стальной литой корпус с промывочной плитой, в пазах которого привариваются лапы, оснащенные шарошками. Шарошки в зависимости от числа конусных поверхностей разделяются на одно-, двух- и трехконусные. Двух- и трехконусные шарошки выполняются самоочищающимися.
В долотах самоочищающегося типа зубчатые венцы одной шарошки заходят в проточки между венцами других шарошек, чем достигается их самоочищение от выбуренной породы. В этих долотах одна из шарошек имеет полный конус, вершина которого заходит за осевую линию долота, а другие две - имеют усеченные конусы.
Трехшарошечные долота, применяемые в зависимости от физико-механических свойств разбуриваемых пород, отличаются друг от друга не только величиной диаметра, но и формой шарошек, шагом и формой зубьев, углом наклона оси шарошки к оси долота, промывочным устройством и размерами присоединительной резьбы.
Опора шарошек является одним из основных узлов долота. Для получения прочности и износостойкости опоры изготавливаются с высокой точностью и прочностью из высоколегированных сталей с термохимической обработкой. Конструкции опор шарошек зависят от типа и размера долот и выполняются в различных вариантах с применением подшипников качения (шарики, цилиндрические ролики) или подшипники качения и скольжения.
Промывочное устройство долот оказывает важное влияние на очистку забоя скважины и зубьев шарошек от разбуренной породы, на степень охлаждения опор и шарошек.
В зависимости от типа и размера трехшарошечного долота промывочные устройства различаются между собой. В отдельных типах долот - промывка центральная с одним каналом, направляющим поток промывочной жидкости по оси долота к центру забоя скважины; в других - с тремя каналами, расположенными в лапах и направляющими поток промывочной жидкости на забой скважины между шарошками; в третьих - с тремя каналами, расположенными в лапах или промывочных плитах и направляющими поток промывочной жидкости - на шарошки. Имеется группа долот с комбинированной промывкой, у которых поток промывочной жидкости направляется между шарошками и на шарошки.
Долота разных типоразмеров выпускаются со вставными штуцерами и без вставных штуцеров.
Долота, у которых струя промывочной жидкости подается к забою скважины и направляется через специальные штуцера (насадки), скорость истечения жидкости из которых значительно повышается, называются гидромониторными. Насадки для гидромониторных долот изготавливаются минералокерамическими и металлокерамическими. Для герметизации зазоров между насадками и промывочным каналом применяются уплотнительные элементы.
При изготовлении долот без штуцеров отверстия выполняются в корпусе долота. В этом случае промывочные каналы образуются по форме внутренней поверхности лап сечениями: круглыми, треугольными и щелевидными.
Штыревые долота предназначаются для бурения в крепких и абразивных породах с высоким сопротивлением сжатию, где проходка долота с обычным вооружением шарошек незначительна. Вооружение шарошек этих долот выполнено в виде вставных зубков - штырей, имеющих рабочую поверхность в форме полусферы.
Долота режущего типа. Долото, разрушающее горную породу резанием и истиранием, называется режущим долотом. Для бурения перемеживающихся мягких, средних и твердых пород в последние годы получили распространение долота режущего типа. Долото истирающе-режущего типа состоит из цельного корпуса, приваренных к нему шести лопастей, из которых три нижние имеют нормальную высоту, а три верхние - укороченную. Каждая укороченная лопасть приваривается между двумя лопастями нормальной высоты. Режущие кромки лопастей скошены и армированы цилиндрическими штырями из металлокерамического сплава. Промежутки между штырями и передние грани всех лопастей армируются зернистым твердым сплавом. В нижней части корпуса, в зависимости от размера долота, имеются от двух до шести промывочных каналов, направление которых предусматривает промывку струей промывочной жидкости забой. У долот гидромониторного типа имеются три промывочных канала, в которые вставляются минералокерамические насадки. Насадки крепятся в корпусе долота при помощи пружинных колец и герметизируются резиновыми кольцами.
Долота алмазные. Алмазным долотом называется режущее долото, армированное алмазами. Алмазные долота предназначены для роторного и турбинного бурения скважин в различных по твердости породах, в которых эффективность применения трехшарошечных долот снижается. Практика бурения подтверждает, что с ростом глубины скважин эффективность применения трехшарошечных долот снижается, и расход их увеличивается. Широко используются алмазные долота при бурении нижних интервалов глубоких скважин. Применение алмазных долот дает возможность увеличить проходку на долото, сократить спускоподъемные операции, получить высокие скорости бурения. Алмазные долота работают по принципу микрорезания и истирания. Интенсивность процесса разрушения горной породы при бурении алмазными долотами находится в зависимости от линейной скорости контакта между алмазами и породой, осевого давления и количества подаваемой промывочной жидкости.
Алмазные долота состоят из фасонной твердосплавной алмазонесущей головки - матрицы и стального корпуса с присоединительной резьбой.
Производительность и устойчивость алмазного долота в основном зависят от свойства и размера применяемых алмазов, схемы размещения алмазных зерен на рабочей части долота и качества изготовления самого долота.
Спиральные алмазные долота предназначены для турбинного бурения. Торцовая часть долота представляет собой три сферические поверхности, оснащенные алмазами. Три промывочные отверстия переходят в сферические спиральные каналы, идущие от центральной части головки к периферии долота.
Радиальные алмазные долота применяются как в роторном, так и в турбинном бурении. Рабочая часть долот выполнена в виде шести секторных выступов, оснащенных алмазами, три малых сектора доходят до промывочного отверстия, а три больших соединяются в центральной конусной части долота. Между тремя большими секторными выступами расположены три отверстия для промывочной жидкости, переходящие к периферийной части в шесть промывочных каналов для отвода промывочной жидкости.
Радиальное алмазное долото предназначено для бурения малоабразивных пород средней твердости.
Алмазные долота с резцами типа PDC. Эти долота предназначены для бурения вертикальных, наклонно-направленых, горизонтальных нефтяных и газовых скважин в малоабразивных породах с промывкой водой или глинистым раствором. Долота армированные зубками PDC, обладают высокой износостойкостью и работоспособностью, а также обеспечивают кратное увеличение проходки за долбление, повышая при этом механическую скорость бурения. Отсутствие движущихся и вращающихся частей продлевает ресурс работы алмазного долота по сравнению с шарошечными долотами.
Бицентричные долота. Бицентричные долота предназначены для бурения с одновременным расширением ствола скважины, в мягких и средних малообразивных горных породах. Применяются для расширения боковых стволов из ранее пробуренных обсаженных скважин, а также расширения в продуктивном интервале с целью увеличения дебита скважины.
Бицентричные долота предоставили возможность бурения скважин большего диаметра, чем обычно возможно при данном диаметре ранее спущенной обсадной колонны. Основные преимущества бицентричных долот: возможность расширения скважин; усовершенствование операций цементирования обсадной колонны; снижение затрат на бурение. Применение бицентричных долот при бурении вертикальных, наклонно-направленных или горизонтальных скважин является новым уровнем в развитии технического прогресса.
Буровые коронки. Буровой коронкой называется породоразрушающий инструмент, предназначенный для разрушения горных пород при бурении с отбором керна. Буровая коронка, армированная резцами из твердых сплавов, называется твердосплавной, а армированная алмазами - алмазной коронкой.
Буровая коронка состоит из короночного кольца, из торца которого зачеканиваются с последующим припаиванием латунью резцы из твердого сплава. Короночные кольца изготавливаются из насосно-компрессорных, бурильных труб или трубных заготовок соответствующего размера.
Твердосплавные резцы, закрепляемые в короночном кольце, должны перекрывать всю площадь торца и выступать за наружную и внутреннюю боковые поверхности и над торцом коронки. Выступающие за наружную поверхность коронки резцы образуют при бурении зазор между коронкой и стенкой скважины. Резцы, выступающие за внутреннюю поверхность коронки, образуют при углублении зазор между керном и внутренней поверхностью колонковой трубы. Выступающие над нижним торцом коронки резцы из твердого сплава непосредственно при бурении разрушают породу на кольцевом забое скважины.
В зависимости от твердости разбуриваемых пород буровые коронки выпускаются для бурения мягких пород, пород средней твердости и твердых пород.
Важными факторами, определяющими конструкцию буровой коронки для бурения различных по твердости пород, являются: величины выхода резцов за наружную и внутреннюю поверхность корпуса и над торцом короночного кольца, угол заострения резцов, форма и расположение резцов.
Для бурения в твердых породах величина выхода резцов внутрь и наружу коронки составляет 0,5-1,0 мм, а над торцом 1,5-2,5 мм.
Расположение резцов относительно торца короночного кольца может быть на одном уровне или ступенчатым. В ступенчатых коронках резцы располагаются как на торцовой поверхности, так и на боковой поверхности на расстоянии 20-30 мм от торца. Это делается для того, чтобы избежать расширения интервала ствола скважины после отбора керна при переходе на долото.
Долота-фрезеры. Долота-фрезеры предназначаются для выполнения вспомогательных работ в процессе бурения и при аварийных работах в скважине.
В зависимости от назначения долота-фрезеры имеют различные формы рабочей поверхности и конструктивно выполняются кольцевыми, торцовыми, фасонными. Они используются для разбуривания обратных клапанов, для истирания металлических предметов, находящихся на забое скважины, для фрезерования оборванных концов бурильного инструмента при аварийных работах, для фрезерования нарушенной части обсадных колонн и других работ.
Широко применяется долото-фрезер типа ФР. Оно состоит из корпуса, имеющего в верхней части присоединительную замковую резьбу. Корпус обтекаемой формы в нижней своей части имеет три выступа, армированных с торца и боковых поверхностей твердосплавными резцами. В нижней части корпуса центральный промывочный канал соединяется с дополнительными каналами, посредством которых промывочная жидкость подводится к различным участкам торцовой части фрезера.
Основные параметры режима бурения сведены в таблицу 2.4.
Таблица 2.4 - Основные параметры режима бурения
Интервал, м |
Скорость вращения, об/мин |
Расход бурового раствора, л/с |
Тип долота |
||
Пилот-ствол |
|||||
III 444.5 М-ГВУ R146 |
|||||
III 295.3 С-ГВ |
|||||
Интервал, м |
Скорость вращения, об/мин |
Расход бурового раствора, л/с |
Тип долота |
||
III 295.3 М-ЦГВ R187 |
|||||
III 295.3 С-ГВ |
|||||
III 295.3 С-ГВ |
|||||
III 295.3 С-ГВ |
|||||
III 215.9 С-ГВУ |
|||||
III 215.9 С-ГВУ |
|||||
Горизонтальный ствол |
|||||